As much of the exterior framing wrapped, the crew worked to begin framing the decks at the east and west entrances to the Cape Cod Hemp House. In keeping with the environmentally friendly intent of this house, this exposed deck framing was done using cedar instead of pressure treated lumber. Cedar is naturally weather-resistant, repels most bugs, and lasts as long as pressure treated lumber.
The crew also continued work on the roof of the connector between buildings by cutting and laying ROCKWOOL insulation. Though a layered application is not required, the crew cut and stacked the ROCKWOOL so that it mimics the pitch of this small roof. They then covered this in plywood, using zip tape to keep moisture out of seams until the Thermoplastic Polyolefin (TPO) rubber roof was installed. Though the rest of the house will receive a zinc roof, this small section will stay rubber as indicated by its slight pitch, which requires rubber for water-tightness.
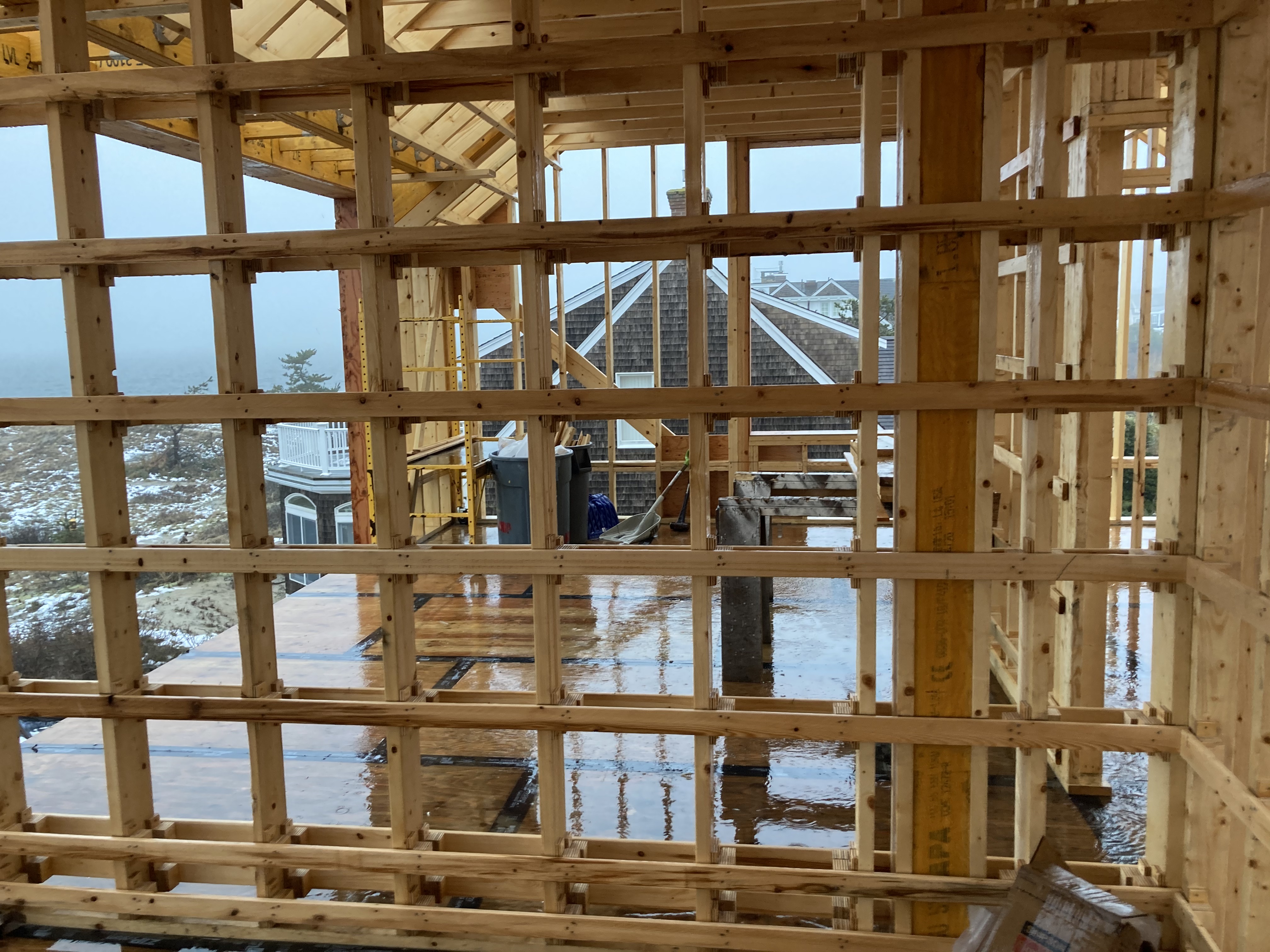
To complement the sound-proofing qualities of the hemp-lime exterior walls, HushFrame soundproofing was installed on all the interior walls at the Cape Cod Hemp House (with the exception of the basement). HushFrames are decoupling devices added to the framing of interior rooms. They are made of sandwiched layers of plywood and silicone, and create a ¼” space between the studs and strapping for the blueboard. As they are made with silicone, they significantly dampen the normal “framing” noise and room-to-room carryover typical in a home. In theory, occupants should be able to blast music in a bedroom without anyone hearing it in the hallway. In a couple of places, the blue board was also doubled up to dampen any sound-travel as well.
At this point, two other concrete features are also being prepped for pouring - the dip pool and the basement egress. Though the formation of the pool’s structure may seem a bit premature, the crew created the formwork for the gunite because of how it fits into the deck’s overall structure. This pool will have headers bolted into the decking, which will rest on a foundation of piers like the rest of the house. The headers must be placed, and formwork pressure tested and inspected before gunite could be poured. The decking also arrived in late February, but will sit tidily in its wrapping for a couple more weeks.
Unlike the pool, once formed and inspected, the bulkhead for the basement egress was poured and backfilled around completing most of the backfill around the house.
As in all projects, work was done simultaneously throughout the house, so while cement work happened at ground level, the crew began installing lath with a ½ inch gap on the underside of the roof rafters to get ready for the arrival of of AKTA, the French Hemp-Lime Guru hired to consult and drive the installation of the hemp-lime insulation at Cape Cod Hemp House. While the original spec was for reed matting instead of lath throughout the house, delays mainly due to COVID-19 caused the team to shift to lath for the roof in order to have a work surface ready prior to Laurent’s arrival which would coincide with that of the matting. More on Laurent, COVID-19, delays and changes in a forthcoming post. The only other place in the house where lathe was used is in the garage.
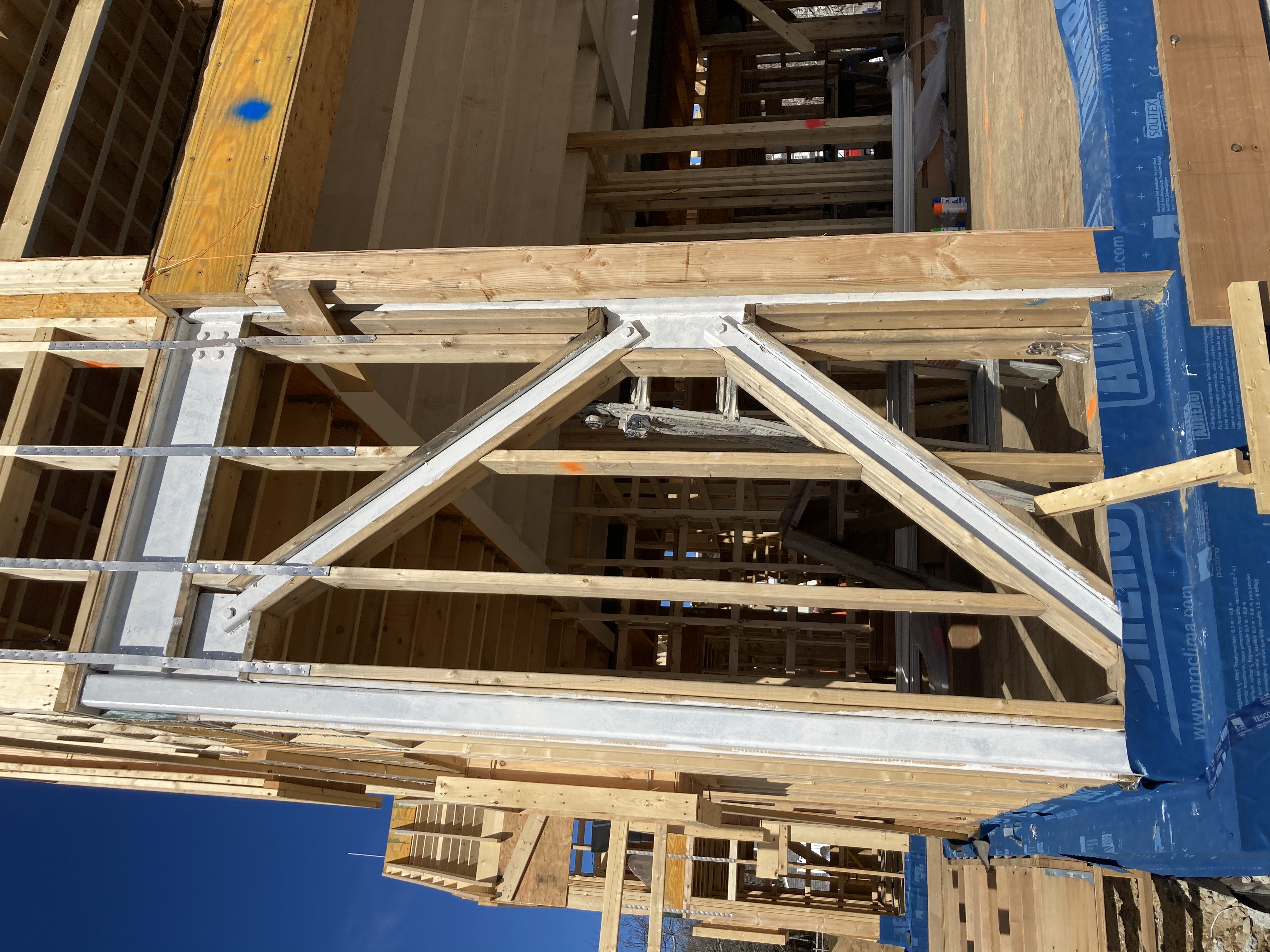
In preparation for the application of hemp-lime, all metal elements which would eventually be exposed to the hemp-lime had to be coated in an epoxy to protect it from the lime, congruent with the spec for stainless steel bolts mentioned earlier. By early March, this was complete and everyone at site was anxious for Laurent’s arrival and to see the hemp-lime for themselves.